Polski przemysł otwiera nowy rozdział, rośnie świadomość konieczności wprowadzenia zmian w związku z postępującą cyfryzacją, wynika z badania NTT DATA Business Solutions
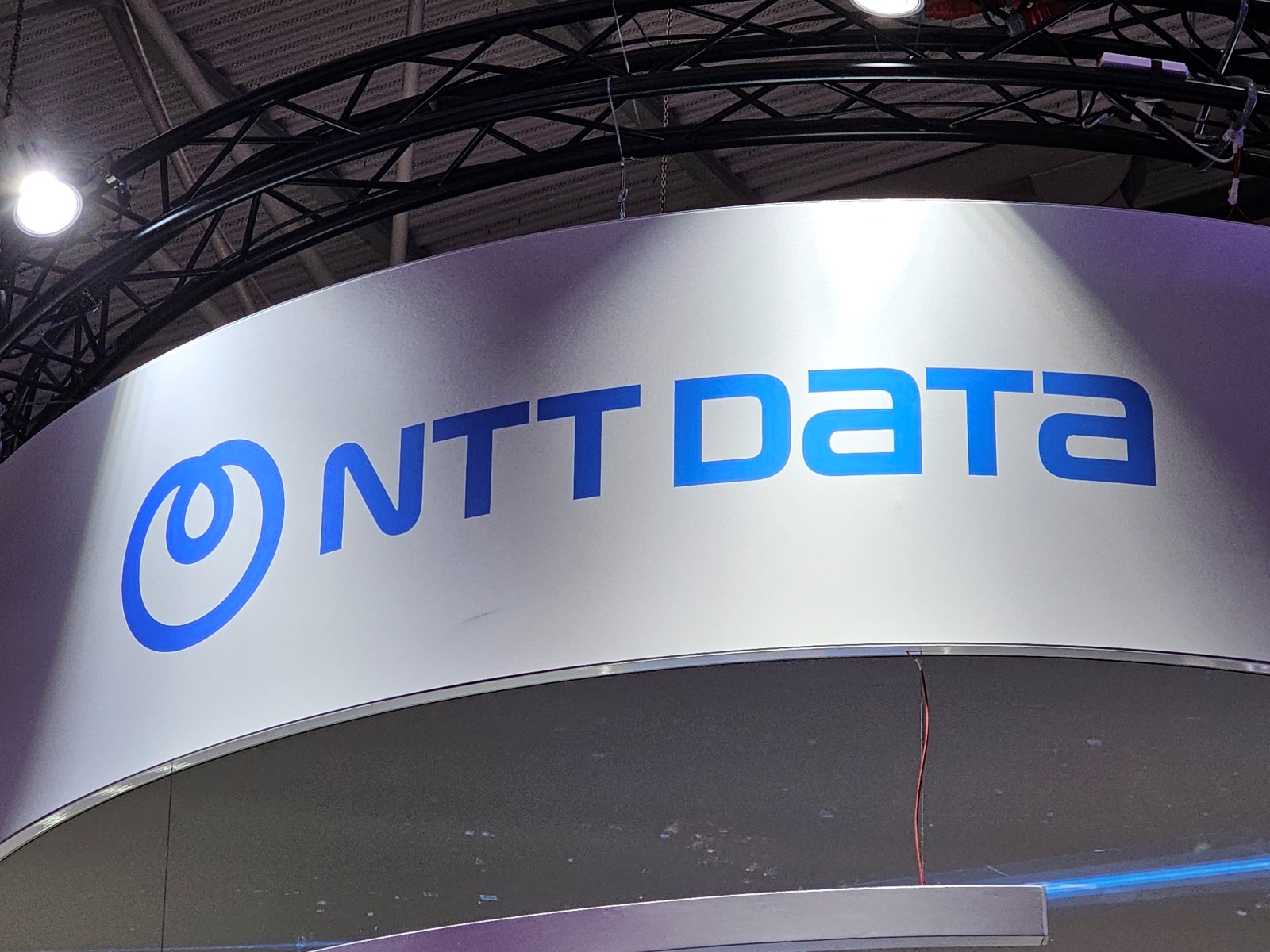
Ponad 7 na 10 (73%) firm produkcyjnych w Polsce dostrzega wyzwanie, jakim są wysokie koszty implementacji systemów IT. Powyższy czynnik wpływa na tempo cyfryzacji w sektorze, jednak badanie przeprowadzone na zlecenie NTT DATA Business Solutions “Cyfryzacja przemysłu: rola zintegrowanych systemów zarządzania w firmach produkcyjnych w Polsce”, ujawnia pozytywny trend – coraz większą świadomość potrzeby zmian. Eksperci podkreślają, że identyfikacja wyzwań to pierwszy krok ku rozwojowi, a digitalizacja procesów to klucz do sprawnego działania biznesów.
Cyfryzacja to dziś naturalny kierunek rozwoju, który może znacząco podnieść efektywność polskiego przemysłu – taką opinię podzielają również sami przedsiębiorcy. Z badania przeprowadzonego przez NTT DATA Business Solutions, firmę specjalizującą się we wdrażaniu systemów ERP i usług managed cloud, wynika, że aż 95% organizacji uważa, że integracja nowych procesów w systemy zarządzania produkcją zwiększa efektywność operacyjną. Tyle samo respondentów uznaje, że rozwój aplikacji biznesowych poprawia przejrzystość procesów, a 84% dostrzega w cyfryzacji możliwość uporządkowania zadań i odpowiedzialności. Mimo pozytywnego nastawienia do innowacji, przedsiębiorstwa podkreślają, że wdrożenie nowych technologii bywa wyzwaniem.
– Dobrze, że firmy produkcyjne mają świadomość swoich ograniczeń, bo to ważny krok do efektywnego planowania rozwoju. Zanim w przedsiębiorstwie zostaną wdrożone nowe technologie, warto zrozumieć, gdzie leżą słabości dotychczasowych rozwiązań i jak wpływają one na codzienną działalność. Tylko taka analiza pozwala na precyzyjne określenie, jakie innowacje są rzeczywiście potrzebne i które inwestycje przyniosą wymierne korzyści. Firmy, które potrafią świadomie podejść do identyfikacji barier i ograniczeń, mogą bardziej trafnie zaplanować cyfryzację, co w efekcie zwiększa szanse na długoterminowy sukces i poprawę efektywności operacyjnej – mówi Piotr Grzegorski, Prezes Zarządu w NTT DATA Business Solutions.
Ponad połowa polskich firm wprowadziła MES mimo obciążeń finansowych – co z resztą?
Na liście barier najwyższe miejsce zajmują kwestie ekonomiczne. 73% firm dostrzega wyzwanie związane z finansowaniem wdrożeń technologicznych. Dla większej części sektora produkcyjno-wytwórczego (74%), wprowadzenie systemu MES (pierwsze wdrożenie, rollout, migracja) wiąże się z wysokimi kosztami. Dochodzą do tego problemy natury ludzkiej (65%), do których zaliczają się między innymi niedobory w kompetencjach pracowników. Jak tłumaczy Piotr Grzegorski nieco większe trudności w tym zakresie spotykają duże przedsiębiorstwa.
– Obecność systemów MES w ponad połowie polskich firm produkcyjnych to pozytywny sygnał świadczący o rosnącej świadomości znaczenia cyfryzacji dla efektywności operacyjnej. Cieszy także to, że 13% deklaruje chęć wdrożenia tego systemu w przeciągu najbliższych trzech lat. Dla wielu organizacji implementacja tego typu rozwiązań pozostaje jednak wyzwaniem finansowym, szczególnie w przypadku dużych firm, gdzie skala i złożoność projektów informatycznych znacząco zwiększają koszty wdrożenia. Przedsiębiorstwa zdeterminowane do wdrażania innowacji, dokładnie planują inwestycje, a czasami dzielą je na etapy. Dla mniejszych firm zaś kluczowe jest szukanie elastycznych rozwiązań wdrożeniowych, które pozwolą im czerpać korzyści z MES bez nadmiernych obciążeń finansowych – komentuje Piotr Grzegorski.
W kwestii modernizacji i rozwoju innych systemów zarządczych oraz produkcyjnych, wyzwania związane z ograniczeniami budżetowymi są wskazywane głównie przez przedstawicieli mniejszych podmiotów (75%) oraz menedżerów niższego szczebla (81%), którzy bezpośrednio odpowiadają za planowanie i realizację prac rozwojowych w systemach IT.
62% firm dostrzega możliwości usprawnienia integracji stosowanych rozwiązań
Nie da się ukryć, że wiele rodzimych firm produkcyjnych napotyka na ograniczenia sprzętowe (46%). Przebrzmiały lub mocno zdywersyfikowany park maszynowy narzuca trudności w integracji z zewnętrznymi systemami informatycznymi. Dla 62% uczestników badania stosowane przez nich rozwiązania są trudne w integracji. Co więcej, 38% menedżerów zauważa w swoim środowisku problemy wydajnościowe, a kolejne 29% – brak oczekiwanej skalowalności infrastruktury.
– Firmy przemysłowe różnią się poziomem przygotowania infrastruktury do obsługi aplikacji biznesowych, co może wpływać na efektywność wdrożeń i skalowalność rozwiązań. Planując inwestycje w licencje, wdrożenia czy rozwój aplikacji, warto uwzględnić potrzebę modernizacji infrastruktury. Bez odpowiednich zasobów technicznych firmy mogą napotkać na ograniczenia wydajności, co utrudni pełne wykorzystanie możliwości nowych rozwiązań. Modernizacja infrastruktury powinna więc być integralną częścią strategii inwestycyjnej, aby aplikacje mogły działać stabilnie i spełniać oczekiwania organizacji. Cieszy fakt, że menedżerowie z optymizmem patrzą na procesowe wsparcie integratora, które ma być kluczem do skutecznej transformacji – mówi Piotr Grzegorski.
Przedsiębiorcy przejrzyście definiują obszary do modernizacji
Zdaniem ekspertów w przygotowywaniach do transformacji cyfrowej przemysłu ważna jest również świadomość tego, jakiego konkretnie rodzaju usprawnienia i wsparcia technologicznego będzie potrzebować dana organizacja.
– Oszacowanie profilu funkcjonalności pozwoli lepiej dostosować system do specyficznych potrzeb firmy, wspierając efektywność, transparentność procesów i możliwość skalowania. Jasno nakreślone wymagania pomogą także w wyborze rozwiązań, które najlepiej odpowiadają długofalowym celom rozwojowym organizacji – radzi Piotr Grzegorski.
W związku z tym, respondenci raportu „Cyfryzacja przemysłu: rola zintegrowanych systemów zarządzania w firmach produkcyjnych w Polsce” widzą największe potrzeby usprawnień w obszarach takich jak planowanie produkcji, sprzedaży i zakupów (55%), analiza kosztów (52%) oraz monitorowanie realizacji produkcji w czasie rzeczywistym (50%). Choć są to kluczowe procesy, które systemy ERP i MES zazwyczaj obejmują, menedżerowie IT dostrzegają możliwość ich dalszego rozwoju, aby zwiększyć efektywność operacyjną i elastyczność działania firm produkcyjnych.
Takich cech oczekują przedsiębiorcy od systemów IT
Aż 83% menedżerów uważa, że współczesny system IT powinien nie tylko zapewniać odpowiedni poziom bezpieczeństwa, ale także elastyczność w reagowaniu na bieżące potrzeby biznesowe. Kluczowe znaczenie ma tutaj pełna integracja sieci IT/OT oraz wdrażanie nowoczesnych technologii, takich jak internet rzeczy i sztuczna inteligencja, w procesy produkcyjne. Z kolei 62% uczestników badania wskazuje, że zintegrowany system zarządzania produkcją powinien zapewniać spójność danych, umożliwiając wszystkim systemom informatycznym korzystanie z jednego, centralnego źródła informacji. Ponadto 59% ankietowanych podkreśla, że implementowany system powinien charakteryzować się łatwością i elastycznością w integracji z istniejącą infrastrukturą.
Natomiast przedstawiciele przemysłu samochodowego (26%) oraz branży spożywczej (również 26%) zdecydowanie częściej niż pozostali ankietowani wskazywali na potrzebę usprawnień w procesach związanych ze śledzeniem przepływu wyrobów i komponentów w ramach gospodarki magazynowej. To bezpośrednia reakcja na zakłócenia globalnych łańcuchów dostaw spowodowane pandemią COVID-19 oraz wojną w Ukrainie.
Powyższe cechy i własne doświadczenia firm z branży produkcyjnej, pozwalają na lepsze zrozumienie swoich potrzeb technologicznych. Dzięki temu będą one mogły skuteczniej pokonywać przyszłe wyzwania rynkowe i zwiększać odporność swoich procesów logistycznych.